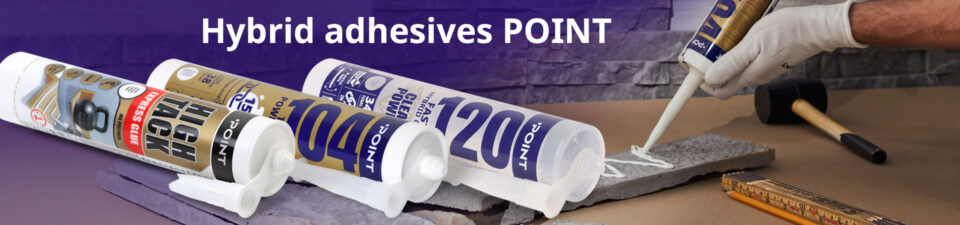
Combining the best properties of traditional adhesives with the latest technology, hybrid adhesives have already become an indispensable tool for specialists. Offering a broader range of applications and greater resistance to temperature, humidity and chemical attack, hybrid adhesives are an excellent choice for construction, repair and furniture manufacturing, as well as for the automotive, electronics and even shipbuilding industries. The hybrid adhesives in the POINT range invite you to experience the unique properties of the products, which have already been appreciated by many professionals and amateurs.
Hybrid adhesives have already made a name for themselves in a wide range of industries and everyday applications, thanks to their many features that are appreciated by specialists, allowing them to work much faster and more efficiently.
“Hybrid adhesives are ideal for joining a wide range of materials – from metal, plastic and glass to wood and composites. This allows them to be used in many different applications, without the need for specialists to use different adhesives for each material,” says Daniel Počikovskij, Product Manager at Tegra State.
Hybrid adhesives also offer excellent resistance to a wide range of external factors such as water, temperature changes, ultraviolet (UV) rays, humidity, chemicals and salty air. This makes them ideal for both indoor and outdoor applications, as well as for industrial applications where resistance to harsh environments is required.
Adhesion and strength, as well as fast drying, are some of the other features that make this product a frequent choice for professionals and amateurs alike.
“Most hybrid adhesives dry quickly, which gives fast results. This makes them suitable for both industrial and repair applications where efficiency and faster turnaround times are needed,” says Počikovskij.
In addition, hybrid adhesives are valued for their flexibility and elasticity, reduced corrosion and oxidation, aesthetic appeal, environmental friendliness and many other benefits.
Recognised by specialists
Although the choice of hybrid adhesives is really wide, Počikovskij suggests to pay attention to a few products of the brand POINT, which are already appreciated by specialists for their uniqueness.
“One of them is POINT 120 Clear Power hybrid adhesive, which so far has no competitors in Lithuania that could be characterised by the same speed and final bonding strength. This clear, ultra-fast curing hybrid adhesive with extreme bonding strength is designed for the fixing of most building materials, including very heavy vertical elements such as ceramic tiles. The adhesive adheres perfectly to metal, aluminium, glass, PVC, polyurethane, concrete and other materials. It can be applied even to wet surfaces, and 70% of the final bonding strength is achieved after only 2 hours,” says Počikovskij while listing the advantages of POINT 120 Clear Power.
Another hybrid adhesive that is recommended is POINT 104 TURBO POWER FIX. This adhesive cures extremely quickly and has an extreme bonding strength of 20 t/m2 after just 15 minutes. POINT 104 TURBO POWER FIX hybrid adhesive is often used for flexible and fast bonding of panels and structures in the construction and metal industry.
POINT High Tack Hybrid Adhesive is also popular with specialists for its very high initial bonding force, which allows even very heavy elements to be bonded without additional support or fixing until dry. The odourless and non-aggressive adhesive, free of isocyanates, phthalates silicone and thinners, is suitable for both indoor and outdoor use, and is also paintable.
How to choose and use?
Daniel Počikovskij, Product Manager at UAB Tegra State, points out that before choosing a hybrid adhesive, it is important to find out the requirements for the application, the environmental conditions, and the mechanical and other properties of the adhesive.
“Hybrid adhesives normally adhere well to most substrates, but some specific materials may not have adhesion, and this needs to be taken into account. When using hybrid adhesives, it is also important to determine the type of joint, whether the joint is rigid or flexible. Hybrid adhesives are well suited for flexible and dynamic joints due to their elasticity, but their elasticity varies. This specification can be checked in the technical product sheets. Specifications such as tensile strength at break and joint flexibility are given in percentages,” says Počikovskij.
The expert notes that before using hybrid adhesives, it is necessary to make sure that they can withstand the expected temperature range, such as extreme heat or cold. Hybrid adhesives typically have a very wide range of temperature resistance after setting – from -40Co to +90Co or even wider.
“For outdoor work, also choose an adhesive with good UV resistance to prevent crumbling. In general, most hybrid adhesives are weather-resistant and suitable for outdoor and indoor use. Another important criterion is the mechanical resistance of the adhesive to the intended load. The bonding strength is usually indicated on the product’s technical data sheet. Although most hybrid adhesives have a high bonding strength, it is not infinite, ranging from 16 to 38 kg/cm2,” he says.
Daniel Počikovskij also recommends taking into account how fast the adhesive cures and whether it fits your schedule. Hybrid adhesives usually have a curing speed of 2–3 mm per day, but there are slower and faster options. This information can be checked in the Technical Data Sheet.
The specialist notes that hybrid adhesives are at the cutting edge of adhesive technology, so it is more difficult to make a mistake with these adhesives than with, for example, acrylic, thinner or polyurethane adhesives. However, it is important to choose the right product for your needs and follow the technical instructions.